Spray Foam Insulation Austin TX
Is your home making you sick? Do you have high energy bills? Are you irritated by uncomfortable rooms? How much pest poop is hiding in your insulation?
Stellrr can transform your home into a comfortable, energy-efficient, and healthy place for your family!
Take action with spray foam insulation Austin TX…
Trustindex verifies that the original source of the review is Google. I want to thank Wayne and Angel for their quick response in helping us out. We were doing a construction project on our student center in San Marcos Tx. and found out that we needed to have a dumpster on site before we could proceed. I made a call to Wayne with dumpstersaurus dumpsters and explained my situation. He was quick to respond and had me a dumpster at the construction site the same day saving us from having the project shut down. Not only did he get it there the same day but the price was very fair and service was very friendly. In today’s business world it was very refreshing to have a company that was trustworthy, quick to respond with same day friendly service, and a very fair price, If you are needing a dumpster I highly recommend dumptersarus dumpsters. Thank you dumpstersaurs dumpsters. Roland M. Roland Merz2025-08-06Trustindex verifies that the original source of the review is Google. Pickle and the entire team did an amazing job from start to finish. From bidding to implementation, they really did the best job. Today our house is cooler than ever! Thanks Stellr! John Farley2025-07-24Trustindex verifies that the original source of the review is Google. Stellr Insulation was fast and efficient. We needed to have a job done quickly and they were very accommodating and even were able to move our appointment up a day. We especially appreciated Pickle as he always kept us informed throughout the process! Ashley Kolar2025-07-02Trustindex verifies that the original source of the review is Google. Very efficient, really friendly service, highly recommend all around Michael Cleveland Osborne2025-06-20Trustindex verifies that the original source of the review is Google. Choosing this company for our attic insulation was a great decision. They got the job done quickly and efficiently, and their team was super organized and professional. Everyone was courteous, and they left the space spotless when they finished. We're really happy with the results, our home feels more comfortable and energy-efficient already. Highly recommend them to anyone looking for quality insulation work! Nathaniel Granger2025-06-12Trustindex verifies that the original source of the review is Google. I had a great experience with Stellrr because the team is awesome. Pickle was so helpful and nice to work with. Frank and Jorge did the insulation work and it went super smoothly. The owner, Wayne, is awesome too - thanks for your extra help, Wayne! Camella Bridges2025-04-27Trustindex verifies that the original source of the review is Google. This is an amazing company! I highly recommend. Stellr has been great to work with. Everyone we were in contact with has been super friendly, polite, and professional. They take the time to explain all of the options for your attic and pricing is straightforward. Sheldon worked with us and he was always so helpful and professional. The two gentleman that came to do the insulation were very hardworking, courteous, and finished ahead of schedule. One of the men even helped bring in a heavy delivery for me- even though he had a huge day of work ahead for him. (I forgot his name, but Stellr knows- because I let them know how impressed I was with his help). The owner Wayne and his wife are wonderful to work with and made sure everything went smoothly. Give these guys a call. Truly excellent company. Laila2025-04-08Trustindex verifies that the original source of the review is Google. I told Stellrr that I would post a review when I had data to back it up. 18 months later, I do: In summer of 2024, we never turned off our A/C. And we saved $1160.71 (58%) vs 2023. This is a likely underestimate of annual savings, since Stellrr installed the foam in May of 2023. I've uploaded a timeline of our gas and electricity bills as we've made multiple improvements--not just spray foam. The gap between what we pay with these improvements and what we would've paid without them will grow bigger forever: energy will never get cheaper. So, here's my empirical take mixed with a bit of common sense: Stellrr's foam insulation provides good value, but without it, other energy-saving improvements will provide half the value they could. It's a foundational improvement--something you do *first*. It's what a nerd's nerd would call "a force multiplier," meaning it makes other improvements vastly more effective by being there. And so you should get it early in your "healthy and efficient home" journey. Unpacking that a bit: from a straight-up balance sheet, we will not ROI on Stellrr, solar, HVAC, electric appliances, and the other improvements we've made. But not breathing all that particulate matter from the nearby interstate? All the gas stove fumes we won't be inhaling? Hell, it's not unlikely we ROI on not having to pay for extended medical care in 30 years. So, if you're into a better quality of life that--bare minimum--mostly pays for itself, I'd recommend doing things In this order: 1. FIRST: Update your ducting, minimally, and your ventilation fans. My only regret--these are hard to do with foam there. 2. Get Stellrr's spray foam. They'll do the best job. 3. Look into a mid-high efficiency heat pump. ($2k tax credit, at least!) Spring a bit extra for an energy-recovery ventilator, installed professionally. Get a UV bulb for that alpine air feeling. 4. Consider solar (30% tax credit til like 2033!)l; also, batteries. 5. If you got those batteries, enroll in Austin Energy's Time of Use program so that you can coast on battery power when electricity is expensive (3-7PM). We do just fine on 20kWh. Bonus: some outage protection! I wasn't the easiest customer--I had a point or two of frustration (communications) with the company during the install. Stellrr sells their product hard, but... like all things ahead of their time, they have to make a complex case that won't appeal to everyone because the value of having an airtight, well-insulated home simply isn't obvious to all. I'm glad I listened--they were right! Joshua Morris2024-12-28Trustindex verifies that the original source of the review is Google. i called to get a quote to top off my attic insulation they call this putting lipstick on a pig! lol had them come out for a diagnostic and they uncovered the real deal about what was going on. i hired them and it took several weeks to get on the schedule to do the work they did a really good job. very happy Taylor Morales2024-01-05Trustindex verifies that the original source of the review is Google. I like working with the Stellrr team on my crawlspace conversión. It was dirty and moldy. Now it is súper clean and I can store my stuff down there. A plus. Albian Barban2024-01-05
About Us
Stellrr is a local company based in Austin focused on making homes better. We transform attics, crawlspaces, and walls to create healthier, more comfortable, and energy-efficient spaces. We reinvest in our community and aim to build a stronger Austin. With over 4,700 clients served and a spotless record, we stand by our honest pricing, experienced team, and dedication to quality work.
Our mission is to cleanse homes and create comfortable spaces where families can thrive. Choose Stellrr for straightforward pricing, reliable service, and lasting results.
Our Services
Residential Insulation
Upgrade your home’s comfort, efficiency, and air quality with our professional insulation services in Austin. Outdated or poorly installed insulation can lead to high energy bills and uncomfortable indoor temperatures. Our expert team provides comprehensive insulation assessments and installs top-quality materials to keep your home consistently comfortable while reducing energy costs. Whether you need an upgrade or insulation for new construction, we’re here to help. Serving Austin and nearby areas, we offer free estimates to make your home more energy-efficient and comfortable year-round.
Contact us today for your free consultation and start saving on energy costs!
Open-Cell Insulation
Open-cell spray foam insulation is an ideal solution for homeowners and commercial property owners in Austin seeking energy efficiency, soundproofing, and cost-effective insulation. Our expert team in Austin specializes in open-cell spray foam insulation services, creating a comfortable living or working environment with excellent thermal performance and reduced energy expenses. Whether your project involves new construction or upgrading existing insulation, open-cell spray foam enhances your property’s efficiency and comfort across Austin and surrounding areas.
Contact us today for a consultation and see how open-cell spray foam can improve your property’s comfort and energy savings!
Closed-Cell Insulation
Transform your Austin property with closed-cell spray foam insulation—a robust choice for thermal protection, enhanced structural integrity, and lasting energy savings. Our Austin-based team delivers insulation services for both residential and commercial properties, ensuring durability, comfort, and efficiency. Whether it’s a new build or upgrading an existing structure in Austin, San Marcos, Round Rock, or Bee Cave, closed-cell spray foam is the reliable solution you need.
Call us today for a consultation and discover how closed-cell spray foam insulation can strengthen and protect your property!
Commercial Building Insulation
Stellrr’s primary focus is on Changing Lives by Cleansing Homes.
But we are properly bonded and insured to handle the paperwork and installation on commercial projects.
We know how much of a pain it is to get commercial work signed off and paid out.
If we decide to take on your project, you can be sure we will see it through to the end regardless of how long the processing takes the “big wigs” to do.
Cellulose Insulation
For properties in Austin, cellulose insulation is a smart, eco-friendly choice that offers excellent thermal resistance, noise reduction, and energy savings. As a leading cellulose insulation contractor in Austin, we provide high-quality insulation services designed to keep your property comfortable, energy-efficient, and environmentally conscious. Whether you are working on a new build or retrofitting an existing home or business, cellulose insulation is a top choice for both residential and commercial applications throughout the Austin area.
Contact us today for a consultation and find out how cellulose insulation can make your property more comfortable and energy-efficient!
Attic Insulation
Converting your traditional vented attic to a spray foam sealed attic will have the biggest impact on your home comfort and energy efficiency.
Required gas utility combustion ventilation is installed to prevent carbon monoxide problems. Then the attic roof deck is spray foamed to R-25 with Icynene GreenGuard Gold Certified Ultra-Low VOC polyurethane. Your thermal and air boundary is moved from your attic floor to the attic roof with high quality products. This moves your HVAC unit out of a hostile 135-degree environment and puts it into a 79-degree semi-conditioned comfy space. With the old insulation gone, and lower energy bills, it is a win-win situation that makes a huge difference.
Crawlspace Insulation
Many homes in Central Texas homes with dirt crawlspaces underneath have mold. Crawl spaces without a vapor barrier naturally have critically high humidity. This results in health problems and structural issues.
Did you know that about 40% of the air you breath in your home comes up from the dirt crawlspace under the house? The nastiness hidden underneath, is in your home also!
How? Ground moisture is wicked up from dirt. This results in the dirt appearing dry. For the first few inches it will be dry because of wicking, but the dirt is moist further down. In homes with a concrete slab, building codes require a 5-mill vapor barrier be installed to prevent moisture infiltration through the concrete, which would ruin wood floors, mold carpet and more.
Insulation Removal
When old or contaminated insulation compromises your property’s efficiency and air quality, professional removal is essential. Our skilled teams use advanced vacuum systems and careful containment procedures to safely extract damaged, moldy, or pest-infested insulation from your attic and walls. We handle the entire process, from thorough removal to proper disposal, preparing your space for fresh, high-performance insulation. Trust our experienced technicians to protect your property and family while delivering a clean slate for your insulation needs.
Schedule your insulation removal assessment today and take the first step toward a healthier, more efficient home!
Wall Insulation
Transform your home’s comfort and energy efficiency with professional wall insulation services from Austin’s trusted experts. Our precision-based approach fills every cavity and void with high-performance insulation materials, creating an effective thermal barrier throughout your living space. Whether you’re dealing with uncomfortable rooms, high energy bills, or outside noise, our wall insulation solutions deliver immediate and long-lasting results. We use minimally invasive techniques to insulate both existing walls and new construction, ensuring your home stays cozy year-round while reducing your energy costs.
Contact us to learn how proper wall insulation can make every room in your home more comfortable and energy-efficient!
Commercial Spray Foam Insulation
When outdated or inefficient insulation affects your building’s energy costs and indoor comfort, professional spray foam installation is the smart solution. Our expert technicians apply high-performance spray foam using advanced equipment to seal gaps, regulate temperatures, and reduce energy waste across warehouses, offices, and retail spaces. We manage the entire process—from surface preparation to precise application—ensuring lasting protection, structural integrity, and improved indoor air quality. Count on our experience to upgrade your facility with reliable, energy-efficient insulation.
Schedule your commercial spray foam assessment today and start optimizing your workspace for savings and comfort!
Residential Spray Foam Insulation
When poor insulation leads to high energy bills and uneven temperatures at home, our residential spray foam services offer lasting relief. Our trained professionals use premium spray foam to seal cracks, insulate hard-to-reach spaces, and create a comfortable, energy-efficient living environment. From attics to crawl spaces, we handle every step—from prep to cleanup—with care and precision. Enjoy quieter rooms, cleaner air, and better comfort year-round with insulation that performs.
Schedule your home spray foam consultation today and take the first step toward a cozier, more cost-efficient home!
What to Expect When Working with Stellrr
- Honest Assessments: Thorough inspection with clear explanations.
- Customized Solutions: Solutions tailored to your home's specific needs.
- Transparent Pricing: No inflated costs or fake discounts.
- Simple Scheduling: Convenient scheduling with clear work details.
- Efficient Work: Quick, precise work with minimal disruption.
- Expert Team: Trained, experienced crews ensuring quality.
- Clear Communication: Regular updates and feedback throughout the project.
- Minimal Disruption: Careful work with thorough cleanup.
- Maintenance and Warranty: Solid warranties with scheduled maintenance.
What Our Customers Say About Us
Trustindex verifies that the original source of the review is Google. I want to thank Wayne and Angel for their quick response in helping us out. We were doing a construction project on our student center in San Marcos Tx. and found out that we needed to have a dumpster on site before we could proceed. I made a call to Wayne with dumpstersaurus dumpsters and explained my situation. He was quick to respond and had me a dumpster at the construction site the same day saving us from having the project shut down. Not only did he get it there the same day but the price was very fair and service was very friendly. In today’s business world it was very refreshing to have a company that was trustworthy, quick to respond with same day friendly service, and a very fair price, If you are needing a dumpster I highly recommend dumptersarus dumpsters. Thank you dumpstersaurs dumpsters. Roland M. Roland Merz2025-08-06Trustindex verifies that the original source of the review is Google. Pickle and the entire team did an amazing job from start to finish. From bidding to implementation, they really did the best job. Today our house is cooler than ever! Thanks Stellr! John Farley2025-07-24Trustindex verifies that the original source of the review is Google. Stellr Insulation was fast and efficient. We needed to have a job done quickly and they were very accommodating and even were able to move our appointment up a day. We especially appreciated Pickle as he always kept us informed throughout the process! Ashley Kolar2025-07-02Trustindex verifies that the original source of the review is Google. Very efficient, really friendly service, highly recommend all around Michael Cleveland Osborne2025-06-20Trustindex verifies that the original source of the review is Google. Choosing this company for our attic insulation was a great decision. They got the job done quickly and efficiently, and their team was super organized and professional. Everyone was courteous, and they left the space spotless when they finished. We're really happy with the results, our home feels more comfortable and energy-efficient already. Highly recommend them to anyone looking for quality insulation work! Nathaniel Granger2025-06-12Trustindex verifies that the original source of the review is Google. I had a great experience with Stellrr because the team is awesome. Pickle was so helpful and nice to work with. Frank and Jorge did the insulation work and it went super smoothly. The owner, Wayne, is awesome too - thanks for your extra help, Wayne! Camella Bridges2025-04-27Trustindex verifies that the original source of the review is Google. This is an amazing company! I highly recommend. Stellr has been great to work with. Everyone we were in contact with has been super friendly, polite, and professional. They take the time to explain all of the options for your attic and pricing is straightforward. Sheldon worked with us and he was always so helpful and professional. The two gentleman that came to do the insulation were very hardworking, courteous, and finished ahead of schedule. One of the men even helped bring in a heavy delivery for me- even though he had a huge day of work ahead for him. (I forgot his name, but Stellr knows- because I let them know how impressed I was with his help). The owner Wayne and his wife are wonderful to work with and made sure everything went smoothly. Give these guys a call. Truly excellent company. Laila2025-04-08Trustindex verifies that the original source of the review is Google. I told Stellrr that I would post a review when I had data to back it up. 18 months later, I do: In summer of 2024, we never turned off our A/C. And we saved $1160.71 (58%) vs 2023. This is a likely underestimate of annual savings, since Stellrr installed the foam in May of 2023. I've uploaded a timeline of our gas and electricity bills as we've made multiple improvements--not just spray foam. The gap between what we pay with these improvements and what we would've paid without them will grow bigger forever: energy will never get cheaper. So, here's my empirical take mixed with a bit of common sense: Stellrr's foam insulation provides good value, but without it, other energy-saving improvements will provide half the value they could. It's a foundational improvement--something you do *first*. It's what a nerd's nerd would call "a force multiplier," meaning it makes other improvements vastly more effective by being there. And so you should get it early in your "healthy and efficient home" journey. Unpacking that a bit: from a straight-up balance sheet, we will not ROI on Stellrr, solar, HVAC, electric appliances, and the other improvements we've made. But not breathing all that particulate matter from the nearby interstate? All the gas stove fumes we won't be inhaling? Hell, it's not unlikely we ROI on not having to pay for extended medical care in 30 years. So, if you're into a better quality of life that--bare minimum--mostly pays for itself, I'd recommend doing things In this order: 1. FIRST: Update your ducting, minimally, and your ventilation fans. My only regret--these are hard to do with foam there. 2. Get Stellrr's spray foam. They'll do the best job. 3. Look into a mid-high efficiency heat pump. ($2k tax credit, at least!) Spring a bit extra for an energy-recovery ventilator, installed professionally. Get a UV bulb for that alpine air feeling. 4. Consider solar (30% tax credit til like 2033!)l; also, batteries. 5. If you got those batteries, enroll in Austin Energy's Time of Use program so that you can coast on battery power when electricity is expensive (3-7PM). We do just fine on 20kWh. Bonus: some outage protection! I wasn't the easiest customer--I had a point or two of frustration (communications) with the company during the install. Stellrr sells their product hard, but... like all things ahead of their time, they have to make a complex case that won't appeal to everyone because the value of having an airtight, well-insulated home simply isn't obvious to all. I'm glad I listened--they were right! Joshua Morris2024-12-28Trustindex verifies that the original source of the review is Google. i called to get a quote to top off my attic insulation they call this putting lipstick on a pig! lol had them come out for a diagnostic and they uncovered the real deal about what was going on. i hired them and it took several weeks to get on the schedule to do the work they did a really good job. very happy Taylor Morales2024-01-05Trustindex verifies that the original source of the review is Google. I like working with the Stellrr team on my crawlspace conversión. It was dirty and moldy. Now it is súper clean and I can store my stuff down there. A plus. Albian Barban2024-01-05
Get The Comfortable and Efficient, Healthy Home You Deserve!
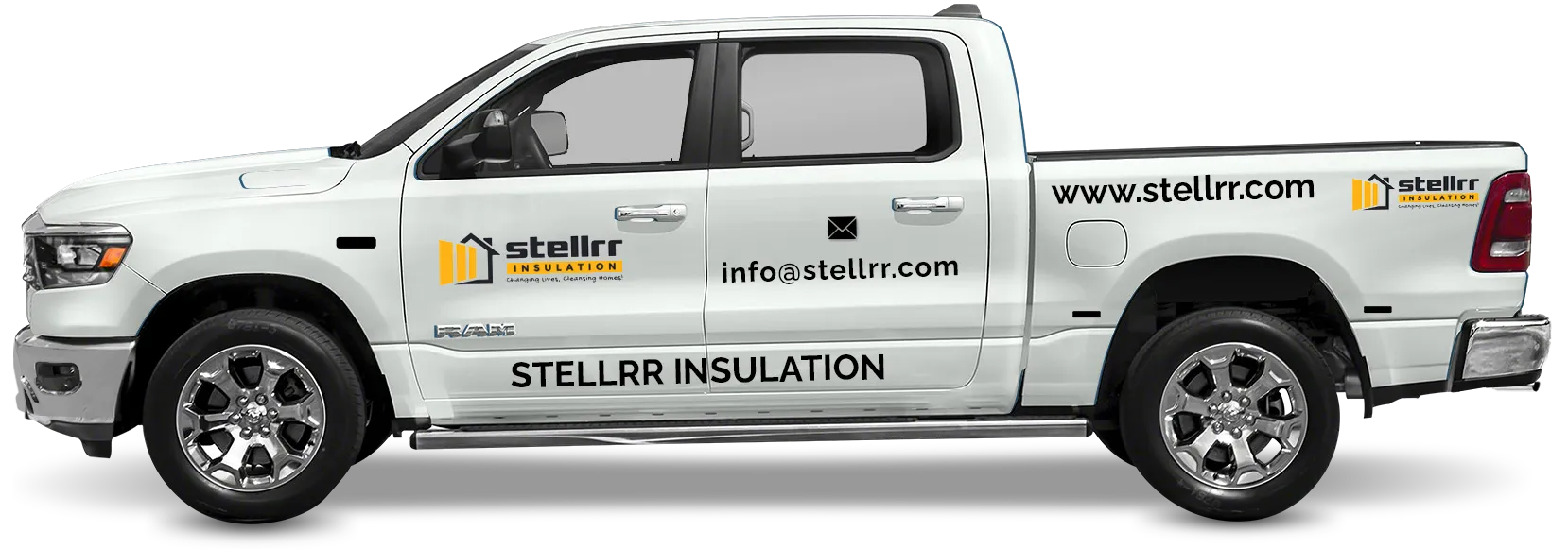
Questions on Spray Foam Insulation Austin
During your consult...
- You will discover precisely what is going on in your home.
- The truth about why you have high energy bills (and how to be energy efficient to lower your utility bills).
- What is the hidden factor in your pest control issues?
- Why are some rooms uncomfortable all the time?
- Where we find the most significant indoor air quality problems.
- The blower door test will reveal air leak locations.
- Your options for fixing the problems (even if it doesn't include hiring Stellrr).
- Thermal imaging shows hot and cold spots.
- Why do Solar, HVAC, & Pest Control pros talk trash about this? (It is incredible how much our work in an Austin home decreases their sales from reduced system requirements.)
- How long it will take to recover your investment (the truth about tax credits).
- And much, much more!
Stellrr is not married to spray foam. We install blown cellulose, Rockwool batt insulation, and other insulation services. Each solution can have a good impact on your energy bills. Many insulation companies only do spray foam or fiberglass. So they only recommend the one they sell. We can get the same results with foam as we can with cellulose. It is about having the whole system installed adequately with quality products.
During your consult, we can compare some of the other insulation options like:
- Installing an aluminum foil radiant barrier.
- Adding a layer of insulation on top of the existing.
- Removing existing traditional insulation materials. Re-blowing new insulation.
- Different types of spray foam systems. How to reduce air leakage with a thick layer of adequate insulation.
- Is foam worth the investment today to lower your carbon footprint?
Most Austin insulation installers make critical mistakes when...
Converting a house from fiberglass into a spray foam encapsulated system. Accidental malpractice is rampant.
Homeowners seldom know of the costly errors until it is too late...
- Homeowners wind up sick with worse allergies and asthma than before.
- Have expensive remediation repairs due to mold or accidentally killing their HVAC.
- Pay serious dough for insulation without improving their comfort or energy bills!
You may have heard the news stories of spray foam insulation poorly done. Bad foam with harmful chemicals is easy to fix in a new build. There is easy access. But correcting a bad foam job with harmful chemicals in an existing home. It is much more expensive for the homeowner.
Stellrr Insulation specializes in converting existing homes into spray foam insulated homes. Most insulation contractors do 95% of new construction. It is simply following the blueprint. But with retrofit homes, we have to redesign everything. And we have to treat the home as a system to impact utility bills, comfort, and make the home healthy. There are...
13-Steps Essential For Success When Converting To Spray Foam Insulation.
I am shocked when I review competitor estimates for Austin spray foam insulation! I rarely see more than 2-3 of the 13 steps included in the proposal. What does it mean? Other foam insulation installers are missing most of the steps for success. Their solution won't save money in the long run. Plus, it can make your home even more uncomfortable, moldy, and allergy-ridden.
What are the 13 essential steps for converting to spray foam insulation?
The 13 steps are a highly guarded secret. Competitors have plagiarized other solutions I shared. I don't worry that competitors would do the 13 steps. It is very difficult to implement. What worries me is they sound competent, which is very misleading.
When you have Stellrr do a home Diagnostic Consult, we will reveal the 13 steps for Success.
In some homes we do not have to preform each of the 13-steps. But we do have to address each one.
Respecting your home is very important to us. We want to leave it better than we found it. Here are some of our insulation installation precautions that others forget:
- Block soffit so it doesn’t spray out the soffit onto your siding ruining it.
- Protect the attic access so we don’t mist inside your house.
- Put down protection for your flooring so we don’t leave a trace.
- Block the gable vents, roof vents, ridge vents so foam does not spray onto your roof.
- Build walls to block the house attic off from the porch attic.
- Build walls to block the garage attic off from the house.
- Install sealed access doors to blocked off areas if access is needed.
- Seal down to the top plate on the house perimeter so it fully stops the air leakage.
Let’s talk more about moisture in the air. Austin is a very humid environment, often 80-90% humidity. This creates a great environment for all sorts of things to grow. If we are constantly bringing in humid air from outside, then we are creating a not so healthy environment inside. We need to seal up the house air leaks not only for energy savings & comfort. But we need to seal up the house for our health. Then we can manage the humidity more effectively. And we can stop mold growth, wood rot, and protect the house structurally.
Check out my video on Fiberglass and Owens Corning. OC sells shingles. OC sells pink fiberglass. They do not want you to buy other products. They want the builder to buy their entire product line. And they trash foam.
The truth about foam is that it does raise the shingle temperature about 5 degrees. But that is it. If shingles cannot handle 5 degrees more heat flow than we get in Austin, then they better not sell shingles in other parts of the country where it is 5 degrees warmer than Austin.
Further, if the foam is “bad” for shingles, why is the owner of the Klaus Roofing franchise network spray-foaming the underside of his roof? I was recently visiting with Klaus Larson at an event and posed this same question to him. He agreed with my statements and shared that the roof on his new, very large home was being foamed as Stellrr does daily.
I foresee that this misinformation that has been spread since the 1980s will begin to change. Why is that? Owens Corning and Johns Manville (the 2 behemoths in roofing) just bought into the foam manufacturing business. I wonder if the old marketing department that trashed foam is still employed?
I double many Austin spray foam insulation contractors will be giving much of their business to JM or OC after the years of misinformation and damages they have caused for us contractors in Austin Texas and around the country.
Does your attic has gas or propane combustion utilities like an HVAC or Water Heater (WH) that use your attic for make-up air to feed the combustion? If yes, then we will have a seperate line item for a Combustion Ventilation Closet for how we handle these items to create a sealed envelope while still bringing in the 1-for-1 make-up air exchange.
If your HVAC or WH flue pipe through the roof is PVC plastic, that is because it is 95% efficient or greater. It means that the unit brings in combustion air through that PVC pipe, and has an inner layer where it exhausts out fumes. These super efficient units reduce energy consumption which means they pair great with foam insulation services.
If you have a metal pipe going out your roof from the WH or HVAC, then you probably have an 80% efficient unit, meaning it requires attic make-up air. So we will have a seperate line item to build out a Combustion Air Closet. The closet will have a zip door on it so that the tech can come in, service the equipment and do any needed work. Then zip it back up upon leaving.
The bottom line is that most spray foam insulation austin contractors don't know how to or are unaware of addressing these factors. The same is true with the misinformation spread by uneducated HVAC technicians.
So if you want an educated and informed insulation contractor, call us today. We are here for all your spray foam insulation work. We will be happy to give you a free estimate for spray foam and other types of insulation materials.
This is the topic most Austin spray foam insulation contractors are deathly afraid of bringing up because it adds cost to the project.
Spray foam is a plastic based material and therefore has a lower smoke, and ignition point than do other materials like Rockwool (which is fireproof).
According to International Residential Code (IRC), spray foam is to be coated with an ignition or thermal barrier under certain conditions.
The spray polyurethane foam we install is Class 1 Fire rated which is the safest class. Commercial buildings require Class 1 Fire rating on materials.
- What does the IRC code want and where?
- What is qualifies as a thermal or ignition barrier?
- Why didn’t Stellrr’s competitors notify me about this building code?
- Do I have to install an intumescent coating? What happens if I decline it?
- What are the alternatives to an intumescent coating?
- What about Appendix X foam that has some ignition barrier in it? Is that good enough?
- What if I wait to have the ignition barrier installed later?
The above questions are answered on the intumescent coating section here.
This code is not unique to spray foam insulation Austin TX. Nope. It is part of the International Building Code.
Great question. This is a common confusion. If done wrong it will cause mold. I done right, it will prevent mold.
Where does this idea come from? Let’s take the mystery out of this cliche. An inefficient house has an HVAC unit sized for that leakage. Say, 1 ton of HVAC per 600 sq ft of home. But when you make the home more efficient, you can move toward 1 ton of HVAC per 800-900 sq ft of home.
The HVAC unit manages the temperature AND THE MOISTURE in the air.
As the HVAC unit runs longer, it removes more moisture from the air. If the home becomes more efficient with the same HVAC unit, it doesn’t run as much. It doesn’t pull as much moisture out of the home’s air.
When your home’s air has more moisture in it, that will start to grow fungal stuff among other things.
So if you make the home more efficient (or spray foam it), you then have to take equal meaasures to manage the humidity separate from the HVAC unit.
In every home that Stellrr converts to spray foam, we insist that the client also has us install a stand alone, whole home dehumidifier in the attic and/or crawlspace.
We install the SaniDry Sedona dehumidifier which adds some “load” back onto the HVAC unit, but it also manages the humidity.
But isn’t it better to just leave the house as it is without energy efficiency upgrades? Nope. Look, if your home is leaky right now, you cannot control the humidity right now either.
Sure in the summer your home will have more regulated humidity, but in the mild months when the HVAC isn’t running much, you will have higher levels of humidity in the air.So that is why it is best to have a SaniDry installed. It will manage the humidity in your home all year long.
So the real solution is to: seal it tight, ventilate it right.
Ideally, we want the humidity in the home to hover around 50%, while 40%-60% is acceptable. Mold doesn’t start growing until you get closer to 80%+. But above 60% is where other things start to grow like dust mites, viruses, and other things.
So the right answer to the question is this: any house, when not properly dehumidified can grow mold. A stand alone whole house dehumidifier should be installed in every central Texas home regardless of getting Austin spray foam insulation or not.
Any insulating material including loose fill fiberglass, cellulose, spray foam and all other attic insulation can contribute to mold when you don't properly manage moisture. The key is to seal it tight, ventilate it right.
Unlike the northern climate zones, in Austin, climate zone 2 uses 1/2-pound open cell spray foam for most stick build wall and attic work.
However, you don't want open cell foam anytime the job has to do with moisture, like in a crawlspace under the home, closed cell is required.
Closed cell spray foam is also the preferred material for metal buildings due to the increasing of the building's racking strength, the water-blocking capabilities, the fact that it is a vapor barrier, air barrier, and the ability to withstand abuse from people and equipment.
A board foot of insulation means 1" thick by 12" wide by 12" long. 1"x12"x12". Closed cell weights about two pounds per cubic foot 12"x12"x12". Open cell weigh about 1/2 pound per cubic foot.
Closed Cell foam insulation cost is about twice that of open cell, but closed cell uses 4x the material. We offer competitive pricing when considering the whole package.
Yes there are people who are uninsured and have no business overhead, and they are cheaper than us. But for many years we have run a top notch company delivering quality service with professional installation, great attention to detail, and a warranty that nobody can beat.
Creating an encapsulated attic addresses the 4 major heat loads on your home that equate to about 50% of the total heat load.
- air seals all attic penetrations
- permanent proper insulation levels
- duct leakage stays in the building envelope
- ducts deliver perfect 55* air in the cooling season (9 months)
Yes spray foam insulation does work.
Stellrr recommends installing R-25 nominal fill of open cell spray foam in attics. Gable walls installed at R-13. This is IECC and COA performance code compliant.
Stellrr installs Huntsman (Icynene) OC No Mix. Icynene is now owned by Huntsman, but the spray insulation formulation is the same. Icynene was started in Canada where the green building and environmental requirements are much higher than in the USA. Which means Icynene formulations are the lowest VOC, healthiest products to have in the home. It is an ultra-low VOC product allowing for 1 hour job site re-entry and 4 hour job site re-occupancy at applicable ventilation rates.
That is as good as it gets when looking for spray foam insulation in Austin. Stellrr is an insulation service that can take care of all your insulation needs. While foam insulation costs are higher than that of loose fill insulation, it is worth it.
Do you need R-49 foam which is the minimum code requirement for blown insulation on the attic floor? You can read about the difference between Prescriptive Code requirements and Performance Code. With foam we are meeting or exceeding the Performance code requirements, so we are doing well at R-25 open cell spray foam on the roof deck.
On Shawn’s personal home, it was built in 2011 by Meritage Homes. Back then, the code requirements were R-20 for the city of Austin. R-20 is just not enough. Shawn was able to take his thermal camera and get significant variances in temperature with the R-20 foam. So he had one of his sprayers add R-5 of Icynene open cell to the existing open cell spray foam insulation. Now the thermal camera registers the entire attic roof as the same temperature.
If you are going to fix your attic insulation and use spray foam Austin and the surrounding areas, then R25 is the way to go.
First the existing insulation is removed. The attic is updated to allow for effective and safe encapsulation. Ensuring bath exhaust fans are ducted outside. Manage any combustion unit make-up air ventilation rooms, build a mesh wall to foam and seal the porches and garage off from the main attic. Next is sterilizing.
Then we install spray foam to the underside of the roof decking. The roof decking is the wood that your shingles are nailed to from the top side. We cover any ridge vents, roof vents, block the soffits, cover the gable end vents, etc. Then we spray the roof, the gable walls, and everything down to the top plate. This seals your attic.
Spray foam insulation installation allows you to then mechanically control the ventilation in your attic giving you control where you had none before.
Seal it Tight. Ventilate it Right. A leaky house is not healthy for you or the house. A sealed house without mechanical ventilation can be troublesome as well. So the answer is to seal it tight so that you can control everything. Then set up the mechanical ventilation so that only “breathes” as much as is necessary.
So what happens if you spray foam my attic, converting it from a vented to an encapsulated attic? Will it be too tight?
No. You will still have leaky walls & windows and bottom plates, and doors opening. This is sufficient. However, you can upgrade your mechanical ventilation, so that you introduce a certain amount of air into your house at set intervals daily. If we are building a combustion closet for you, we are still bringing in fresh (make up) air into that closet, so fresh air will be introduced. But you can also have what is called an Energy Recovery Ventilator (ERV). ERVs are a luxury and rarely installed even in new custom build homes.
Your tight house will now allow you to manage the humidity inside the house. One way of managing the humidity is through our SaniDry dehumidifier system.
Also, we are usually installing open cell spray foam in an attic. With our vapor diffusion ports, the attic is still able to breathe even with the air sealing. Vapor barriers are not ideal in Austin area attics. But vapor barriers are essential under homes in crawlspaces.
My childhood home, mentioned in the paragraphs above, had the roof replaced just before my parents sold it. The house was 20 years old and had been foamed. Of the entire house, there was part of a sheet of decking that needed replacing. The decking was in a valley and had some rot. It came up without damaging the foam and was replaced. Easy.
I’ve asked several of my roofing friends about their real world experience here. They say that open cell foamed roofs DO allow them to find leaks. The open cell is porous and allows moisture to come through close to the leak location.
They say that only 3-5% of roofs need any decking replaced, and at that, it is usually only a sheet of decking regardless if it is a blown in roof for spray polyurethane foam insulation roof.
If you have to have your roof replaced, it will probably be done with insurance money. So if any foam has to be repaired or replaced, the insurance will cover that as well. But guess how many calls or jobs we have done to repair foam after a roof replacement? We did one job years ago. And it was not because the foam needed repairing. The foam was attached directly to the metal roof. The metal roof was damaged when their carport was blown onto the roof and dented it badly. The roof was able to be removed without damaging the closed cell foam. The building owner wanted to replace the foam because he didn’t like the job my competitor did, and he wanted it to look pretty. So he hired us to re-do the foam 100% since it was a metal building with exposed foam.
Call us for a free estimate.
Need your HVAC or Water Heater replaced?
Great! Now you can upgrade to a more efficient and smaller air conditioning unit that will lower your energy costs even more. That means that the Combustion Air Closet is no longer needed. It can be demolished in less than 2 minutes with a baseball batt or 10 minutes with a hand saw. Very easy. Now your new unit can go in with zero obstructions.
Need your HVAC or WH replaced?
Once your attic is converted from blown insulation on the attic floor, to foam on the attic ceiling, it is a worker's dream come true.
The problem with blown insulation on the attic floor is it is always in the way of any work needing to be done. Technicians will damage the blown insulation walking through your attic to run wires, fix plumbing, check the HVAC, or Water Heater, etc. The same thing with pests, they scurry through and damage the insulation.
However, a foamed roof is up and out of the way. There is clean and clear access for whatever work a technician needs to do. It is also a cool safe environment for them to work. If you ever have pests enter the attic, you will hear them loud and clear walking on your Sheetrock. Then with a clean, clear attic, you can find them and get rid of them asap.
Growing up, the house I lived in had a spray foamed roof. I had access to storage that was exposed to the foam roof. Never once did I see any of the foam damaged in my childhood home. My parents sold their home a few years ago, 20 years after building it. When we were prepping it for sale, I inspected all of the foam insulation, but still no damage. Perfect condition. But can you imagine if it was blown insulation? It would be a disaster.
We install foam on the underside of the roof deck and gable walls over the conditioned space. We block off the porch and garage. If we are spraying the garage, it will be a separate line item for installing spray foam insulation.
Our quotes are based on the Central Appraisal District footprint of the house, plus the roof pitch.
The garage and porches are always a separate line item on the CAD, and thus if we are insulating them, it is a separate line item there too.
If the house attic is shared with the garage attic, the code requires that the house attic be separated from the garage attic even if we are also foaming the garage. Why? They want to prevent any potential vapor from the garage going over into the house. So we build a mesh wall, install a zip door, and then foam the wall to separate it from air and moisture infiltration.
You may hear people talking about SPF and SF.
Spray Polyurethane Foam and Spray Foam is like saying hand me a 2"x4" vs saying hand me a 2"x4"x8' stud.
All high pressure foam that professionals install is a polyurethane. Poly means multi or plural. SPF or SF has two components. An A side barrel and a B side barrel.
These two barrels and the materials inside much stay separated at all times until they come together in the tip of the gun (plural component dispensing unit).
When the two come together in the gun, under the right pressure, hot air temperature, ratio, and with the proper substrate preparation, it is sprayed out at over 1,000 psi. At that time it mixes, chemically reacts, hot air off gasses, expanding and makes polyurethane foam insulation. The reaction time of SPF is just a few seconds.
SPF is harmless once turned into a solid. Most foams are water blown these days. So the B side, the Resin, is partly Water, along with the other secret components that make it expand. Years ago spray foam contained CFCs, HFOs, and other blowing agents that were an environmental concern.
However SPF installation can be very dangerous when near the materials in their raw form. The A side is like superglue. If a drip gets in your eye, it is hospital time because it will crystalize when it hits water. So anytime you are messing with the raw components of SPF, make sure you have full PPE!
Enhancing Energy Efficiency with Comprehensive Spray Foam Insulation Reviews and Installation Techniques
SERVICE AREA: Stellrr offices are in South Austin Texas, but we have a wide service area. We were founded by and still are Austin-owned and operated by the Mansur family. You can find Stellrr on the major review sites: Houzz, Yelp, BBB, Porch, HomeAdvisor, and find Shawn’s personal Linkedin here. We regularly take on projects from Taylor to Bastrop to Canyon Lake to Fredericksburg to Marble Falls. Yes that includes Round Rock, Cedar Park, Lakeway, Dripping Springs, San Marcos, Canyon Lake, Elgin, Pflugerville, Leander, Spicewood, and so much more in the Austin area. So if you are within 60 miles of Austin, we can help you out. There is hope if you are outside the area, like in San Antonio. We will travel for the right project. Let’s talk about it.
Stellrr Insulation & Spray Foam is located on 401 Congress Ave, #1540, Austin, TX. From Austin-Bergstrom International Airport (AUS) take Hotel Dr to State Hwy 71 W/E Ben White Blvd, and head southwest on Presidential Blvd toward Service Dr. Then slight right onto Service Dr, and turn right onto Hotel Dr. Next turn right onto Spirit of Texas Dr, and turn left to merge onto State Hwy 71 W. Afterwards, keep left to stay on State Hwy 71 W, and continue on State Hwy 71 W/E Ben White Blvd to N Interstate 35 Frontage Rd. At this point take exit 233 from I-35 N/US-290 E, and keep left to continue on State Hwy 71 W/E Ben White Blvd. After that use the right 2 lanes to merge onto I-35 N/US-290 E toward Waco, and take exit 233 toward Riverside Dr. Then take E Riverside Dr and S Congress Ave to E 4th St, and merge onto N Interstate 35 Frontage Rd. Next use the left 2 lanes to turn left onto E Riverside Dr, and turn right onto S Congress Ave. Finally, turn right onto E 4th St, and Stellrr Insulation & Spray Foam will be on the left.
We’re open: Monday-Sunday 6AM – 10PM
For additional questions, you can call us at (512) 710-2839 or find us on yelp
Loading map...
Comprehensive Spray Foam Installation Services: Enhancing Your Home’s Efficiency
At Stellrr our mission is to Change Lives by Cleansing homes. We are serious about listening to what you want us to accomplish for you. When we do a full Space Age Cleanse, we guarantee the results we promise and we offer a lifetime warranty. We actively monitor how our system is working in your home to ensure everything is as promised, and should a problem ever arise, we can catch it before it turns into something big.
This is the level of service you get with our Space Age Cleanse and we also have an incredible performance guarantee with our full CrawlSpace Cleanse. Sure other companies can offer similar or better prices on aspects of the entire system. But you won’t find anyone who stands behind their installed system like we do.
In fact, if you can find someone who has a stronger system performance guarantee and lifetime warranty, I’ll pay you $500, even if you don’t hire Stellrr. – Shawn, Founder and Author
Choosing the Right Insulation: Fiberglass Insulation vs. Spray Foam Insulation Installation
Choosing the right insulation involves comparing fiberglass and spray foam options. Fiberglass is cost-effective and easy to install, making it ideal for traditional projects. Spray foam, however, offers superior air sealing and energy savings by expanding into gaps to create an airtight seal. Whether working with insulation work specialists or spray foam contractors, understanding each type’s benefits helps make an informed decision to enhance your property’s efficiency.
Benefits of Open Cell Spray Foam and Closed Cell Spray Foam in Home Insulation
The benefits of incorporating both open cell and closed cell spray foam in home insulation are substantial, especially when optimizing for both comfort and energy efficiency. Open cell spray foam, a lighter variant of spray polyurethane foam, is excellent for indoor applications such as office spray foam insulation. It expands greatly upon application, effectively sealing air leaks and enhancing the overall insulation system of a building. This makes it ideal for an insulation upgrade where acoustic properties and breathability are priorities.
Conversely, closed cell foam is a denser type of spray polyurethane foam that acts as a powerful foam insulator, providing a higher R-value per inch than open cell foam. This characteristic makes it suitable for external areas or locations requiring robust insulation against moisture and air infiltration. Utilizing a qualified spray foam insulation contractor can ensure that both types of foam are appropriately installed to form a comprehensive spray foam insulation system. This approach maximizes thermal efficiency and contributes to significant energy savings over time.